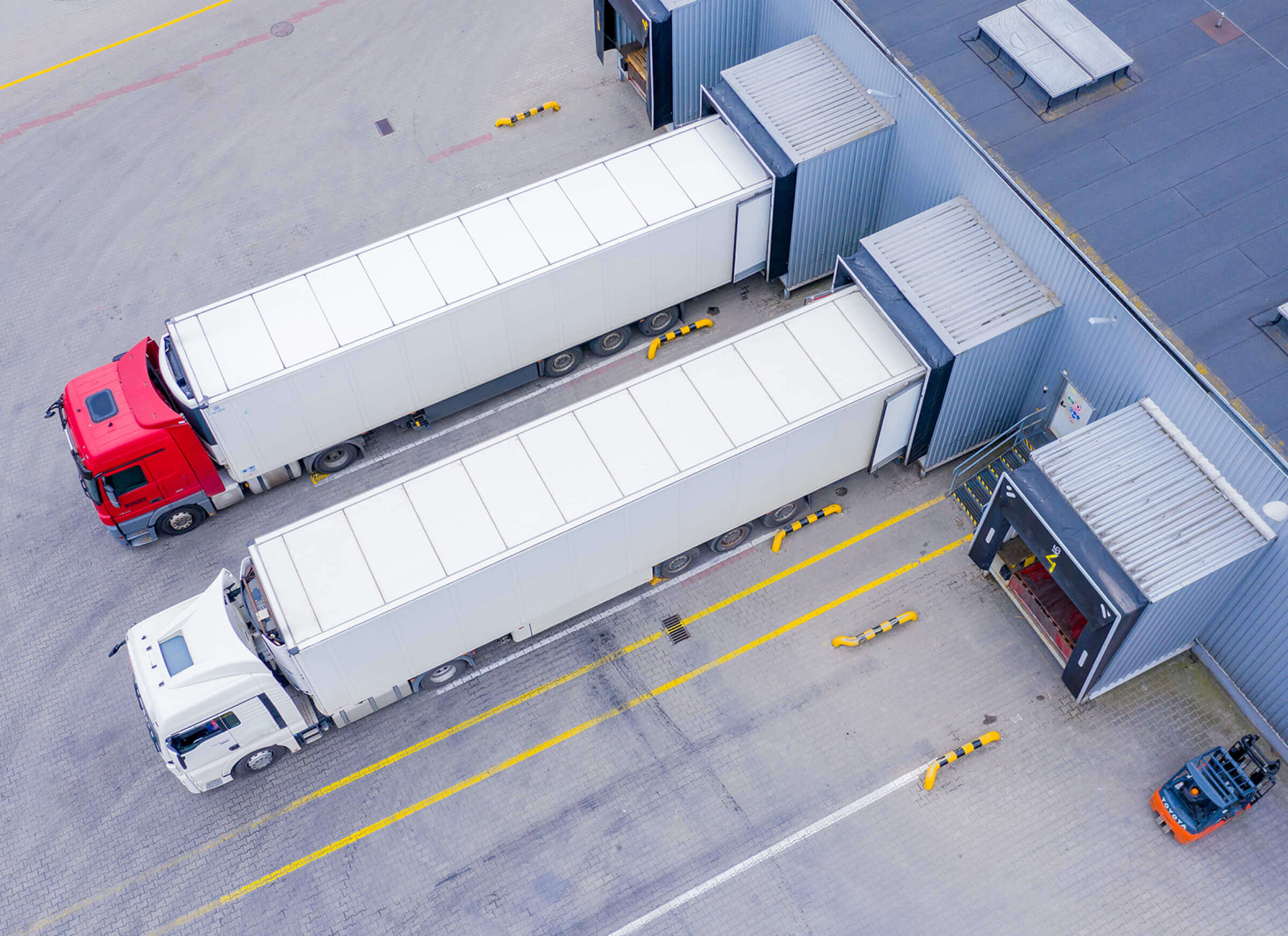
Cross-docking is a logistics process where goods are quickly moved from incoming transportation to outgoing shipments without significant storage. This approach differs from traditional warehousing, as it prioritizes efficiency by reducing the time products spend in storage or transit. Cross-docking is widely used in industries with fast-moving supply chains, such as retail, e-commerce, and perishable goods.
The Definition of Cross-Docking
At its core, cross-docking is the practice of unloading materials from incoming trucks or railcars and directly loading them onto outbound transportation vehicles. The process bypasses traditional warehousing by sorting, consolidating, or deconsolidating shipments as needed. This system allows businesses to streamline their supply chains, cut down on storage costs, and improve delivery times.
Cross-docking is particularly beneficial in just-in-time (JIT) supply chains, where the timely delivery of goods is essential for operational efficiency. It eliminates the need for large storage facilities, replacing them with distribution hubs designed for quick turnover.
Types of Cross-Docking
Cross-docking can be categorized into several types based on its application and the specific industry needs:
- Manufacturing Cross-Docking. This type is used in manufacturing industries to consolidate components needed for production. Suppliers deliver parts to a facility where they are directly transferred to the production line.
- Retail Cross-Docking. Ideal for retail chains, this type involves consolidating goods from multiple suppliers at a distribution center. The consolidated shipments are then sent to individual retail stores.
- Distributor Cross-Docking. Distributors use this approach to receive products from multiple manufacturers and create a single shipment for their customers.
- Transportation Cross-Docking. This type involves consolidating shipments from multiple carriers to optimize outbound transportation. It is commonly used in freight forwarding and logistics companies.
- Opportunistic Cross-Docking. This type is performed when an immediate need arises for a specific product at a nearby location, often in emergency or special circumstances.
The Benefits of Cross-Docking
The implementation of cross-docking offers numerous advantages that can significantly enhance supply chain efficiency:
- Reduced Warehousing Costs. Eliminates or minimizes the need for long-term storage facilities. Lower expenses related to inventory management, such as utilities and labor.
- Improved Delivery Speed. Reduces the time products spend in the supply chain. Enhances the ability to meet customer demands for faster delivery.
- Lower Inventory Holding Costs. Minimizes inventory levels and associated risks like obsolescence or damage. Frees up capital tied in inventory storage.
- Increased Transportation Efficiency. Consolidation of shipments results in optimized transportation routes and reduced costs. Enhances truckload utilization, reducing the number of trips and associated emissions.
- Better Product Handling. Reduces the risk of product damage as goods are handled fewer times. Maintains the quality of sensitive items, such as perishable goods.
The Risks and Challenges of Cross-Docking
While cross-docking offers many benefits, it also presents several risks and challenges that businesses must address:
- Initial Setup Costs. Requires investment in infrastructure, technology, and training. The setup of distribution hubs and integration with supply chain systems can be costly.
- Dependency on Technology. Efficient cross-docking relies on advanced logistics software for real-time tracking and inventory management. System failures or technological issues can disrupt operations.
- Coordination Challenges. Requires seamless communication between suppliers, carriers, and distribution centers. Miscommunication can lead to delays or errors.
- Limited Application. Not suitable for all industries or products, particularly those with low turnover rates. Goods requiring long-term storage or specific conditions may not benefit from cross-docking.
- Risk of Stockouts. With minimal inventory on hand, businesses face a higher risk of stockouts during supply chain disruptions.
Cross-Docking Process
The cross-docking process involves several key steps that ensure the smooth transition of goods from inbound to outbound transportation:
- Receiving. Goods arrive at the distribution center via inbound trucks or railcars. Products are unloaded, inspected, and sorted.
- Sorting and Consolidation. Items are grouped based on their destination or specific customer requirements. Consolidation may involve combining products from multiple suppliers into a single shipment.
- Loading and Shipping. Consolidated shipments are loaded onto outbound trucks or railcars. Goods are dispatched to their final destination, ensuring timely delivery.
Industries That Benefit from Cross-Docking
Cross-docking is widely used across various industries to improve supply chain efficiency:
- Retail. Allows retailers to meet customer demands for faster delivery times. Reduces storage requirements for seasonal or high-turnover products.
- E-commerce. Enhances the ability to handle large volumes of orders with minimal lead time. Supports same-day or next-day delivery models.
- Food and Beverage. Essential for perishable goods with a limited shelf life. Maintains product freshness and quality by reducing handling time.
- Pharmaceuticals. Ensures the timely delivery of sensitive products requiring specific conditions. Reduces the risk of product degradation.
- Automotive. Facilitates the JIT delivery of components to assembly lines. Minimizes production delays caused by inventory shortages.
Technology in Cross-Docking
Modern technology plays a crucial role in enabling efficient cross-docking operations. Key technologies include:
- Warehouse Management Systems (WMS). Automates sorting, consolidation, and inventory tracking. Provides real-time visibility into supply chain activities.
- Transportation Management Systems (TMS). Optimizes route planning and carrier selection. Ensures timely coordination between inbound and outbound shipments.
- Barcode Scanning and RFID. Enhances accuracy in tracking goods throughout the cross-docking process. Reduces the risk of errors and misplacements.
- Advanced Analytics. Provides insights into supply chain performance and areas for improvement. Helps identify trends and forecast demand.
Best Practices for Implementing Cross-Docking
To successfully implement cross-docking, businesses should follow these best practices:
- Evaluate Suitability. Assess whether cross-docking aligns with your supply chain needs and product characteristics.
- Invest in Technology. Deploy advanced logistics systems to streamline operations and enhance coordination.
- Choose Strategic Locations. Establish distribution hubs close to suppliers and customers to minimize transportation time.
- Train Staff. Provide training on cross-docking processes and technology to ensure operational efficiency.
- Monitor Performance. Regularly evaluate cross-docking activities to identify and address inefficiencies.
Cross-docking is a transformative logistics strategy that enables businesses to streamline their supply chains, reduce costs, and improve delivery times. While it offers numerous advantages, successful implementation requires careful planning, investment in technology, and effective coordination. By understanding the types, benefits, and challenges of cross-docking, businesses can determine whether this approach aligns with their operational goals and customer expectations. As supply chains continue to evolve, cross-docking will remain a vital tool for achieving efficiency and competitiveness in the logistics industry.